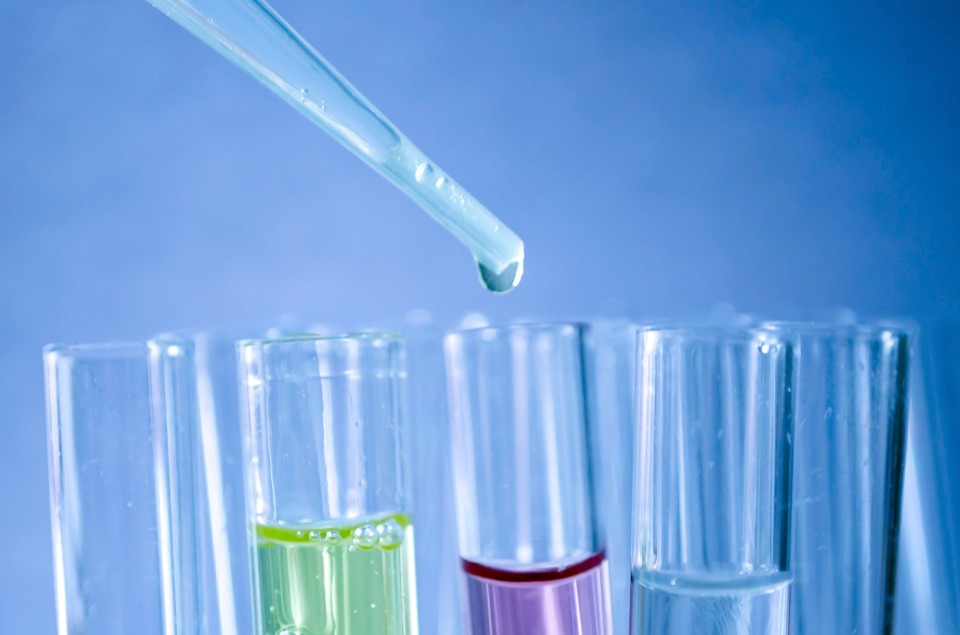
The most important stage of preparing heterogeneous catalysts for carbon nanomaterial (CNM) is their activation, which is understood as a complex of physical influence on the catalytic material, which allows to significantly increase the efficiency of nanostructure synthesis.
This can be achieved by researching mechanical (dispersion) and physical (electromagnetic and ultrasonic) activation methods.
One of the most important factors defining catalyst efficiency is its granulometric composition. It is known that reduction of the particle size (less than 3 nanometers) causes capsulation inside nanotubes, while increasing it above 25 nanometers leads to uneven size distribution and defects in nanotubes. This is due to the fact the using large catalyst particles (25 to 100 nanometers) prevents carbon scattering from the surfaces where hydrocarbon decay occurs to the surfaces where carbon is deposited; as a consequence, no CNM growth occurs on such particles. Therefore, it is important to define reasonable catalyst particle size, as well as dispersion and classification methods.
Note that dispersion of catalyst microparticles causes both the reduction of size and the changes in the microstructure, e.g. destruction and reduction of pore depth, increasing the boundary of nano-seeds, where graphitized carbon is deposited.
Catalyst was activated in a drum mill and an electromagnetic vortex layer device (AVS). The distinguishing characteristic of the vortex layer in electromagnetic units is the multitude of high frequency and strength shocks, as well as friction, which not only break solid particles, but significantly activate their surfaces due to the deformation of their crystalline lattice. Enormous energy is concentrated in a volume of this process, which direct influence on the material. The influence is so high that it changes the structure as deeply as the atom’s valency shells. The process causes deep changes in the structure of the material.
Mean energy conducted to a volume of the vortex layer reaches 103 kW/m3. This is several orders of magnitude higher than in vibration mills, for instance. Besides, the energy is localized in certain areas, e.g. in the locations where the ferromagnetic particles collide, where mean power reaches even higher.
The electromagnetic vortex layer unit consisted of a process section and a control section, connected by oil tubes and a power cable. The process section consisted of a support, an enclosure, an induction coil for the rotating electromagnetic field, and a detachable operating chamber.
The catalyst activation process was performed with 1…1.5 mm by 10…15 mm PVC encapsulated ferromagnetic particles.
The chamber was loaded with 0.120 kg of the catalyst and 0.060 kg of ferromagnetic particles; retention time varied from 5 to 60 seconds. The granulometric composition of the Ni/MgO catalyst after the dispersion was done by fractionating sieve analysis. The catalyst after activation was separated into fractions and used for CNM synthesis under a unified method of testing various catalyst samples.
The results of the experiment show that the optimal duration time for the finest grinding constitutes 10 seconds, with initial catalyst particle size of 500 micron.
The observed increase of catalyst particle size after 10 or more seconds of dispersion is apparently due to the fact that with time the particles accumulate sufficient energy for spontaneous aggregation.
The analysis of the influence of the catalyst size composition on the mean output of CNM leads to the conclusion: the output increases in inverse proportion to catalyst particle size. This is due to the increased active surface of the catalyst. The experiments demonstrated that the actual method of catalyst dispersion has no significant influence on nanomaterial output.