A huge amount of water is consumed in electroplating workshops. Most of the volume is used to prepare and adjust electrolyte and for rinsing products after processing.
Depending on the type of contaminants the wastewater from electroplating plants is divided into three groups:
- The acid-alkaline water. It contains acid (sulfuric, hydrochloric, nitric, hydrofluoric), alkali and heavy metal ions (copper, nickel, cadmium, iron, zinc, tin, lead). pH indicator for such drainage ranges 1 -10;
- Cyanide-containing wastewater. It contains free cyanide, zinc cyanide compound, copper, cadmium and various salts. Acidity of cyanide drains usually exceeds mark “7”;
- Chromium-containing water. The composition of chromium-containing drainage include trivalent chromium, iron, zinc, copper, nickel, chromates and acids. The acidity of wastewater can vary from 1 to 7.
Neutralization of cyanide and chromium-containing wastewater is recommended to be done separately as they release toxic hydrogen cyanide in the case of co-processing. The same reason prevents mixing cyanide containing wastewater with acid.
Cyanide wastewater treatment may be achieved using reagent, ion exchange or electrochemical method. Also possible to use ozonation and hyperfiltration.
In fighting cyanide more commonly is used a modification of reagent and electrochemical methods. Modified reagent method chemically converts highly toxic cyanide into non-toxic and manageable products. For oxidation there are used KMnO4, H2O2, O2, O3 и Cl.
Already there are successful experiences in the application of vortex type grid chambers in wastewater treatment processes. Their effectiveness is due to a number of factors:
- Electromagnetic treatment and substance activation;
- Dispersing phase;
- Operation of the vortex layer, its hydrodynamic factors that provide an intensive mixing of the processed materials.
Various waste compositions require further testing to investigate the effectiveness of performance and future application in each separate case.
GlobeCore cleaned cyanide-containing wastewater sample on the vortex type machine vortex layer device AVS 150. 0.5 L of water was taken with 250 g of dipole particles of ferromagnetic steel 08G2S 2 mm diameter and 20 mm long. The reagent used – was sodium hypochlorite NaCl with active chlorine concentration of 190 g / l. The initial zinc content in the drainage was 24 mg / l.
Then 66 mg of sodium hypochlorite was added to the liquid to be processes with, representing 100% of the stoichiometric ratio. The level of acidity during cleaning process was pH = 10.4. The processing time in the machine was 3 seconds.
After cleaning , the results showed :
- cyanide content of less than 0.005 mg / liter;
- the chlorine residue content is less than 2 mg / l.
To compare the results achieved using vortex layer device GlobeСore AVS-150, a similar experiment was conducted with a stirring device. It was established that using vortex layer unit completes the deposition of cyanide in less than an hour, and using a stirring device – more than six hours. The sediment obtained by treating wastewater in the vortex layer unit, proved to be more dense, due to the magnetization of the ferromagnetic ground particles.
Chlorine content in the drainage after a stirring device was 6 mg / l, which is three times more than after vortex layer device AVS-150.
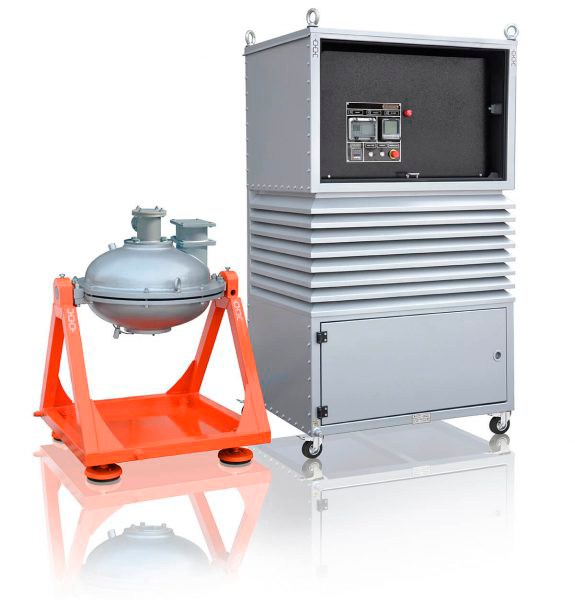
cyanide wastewater treatment